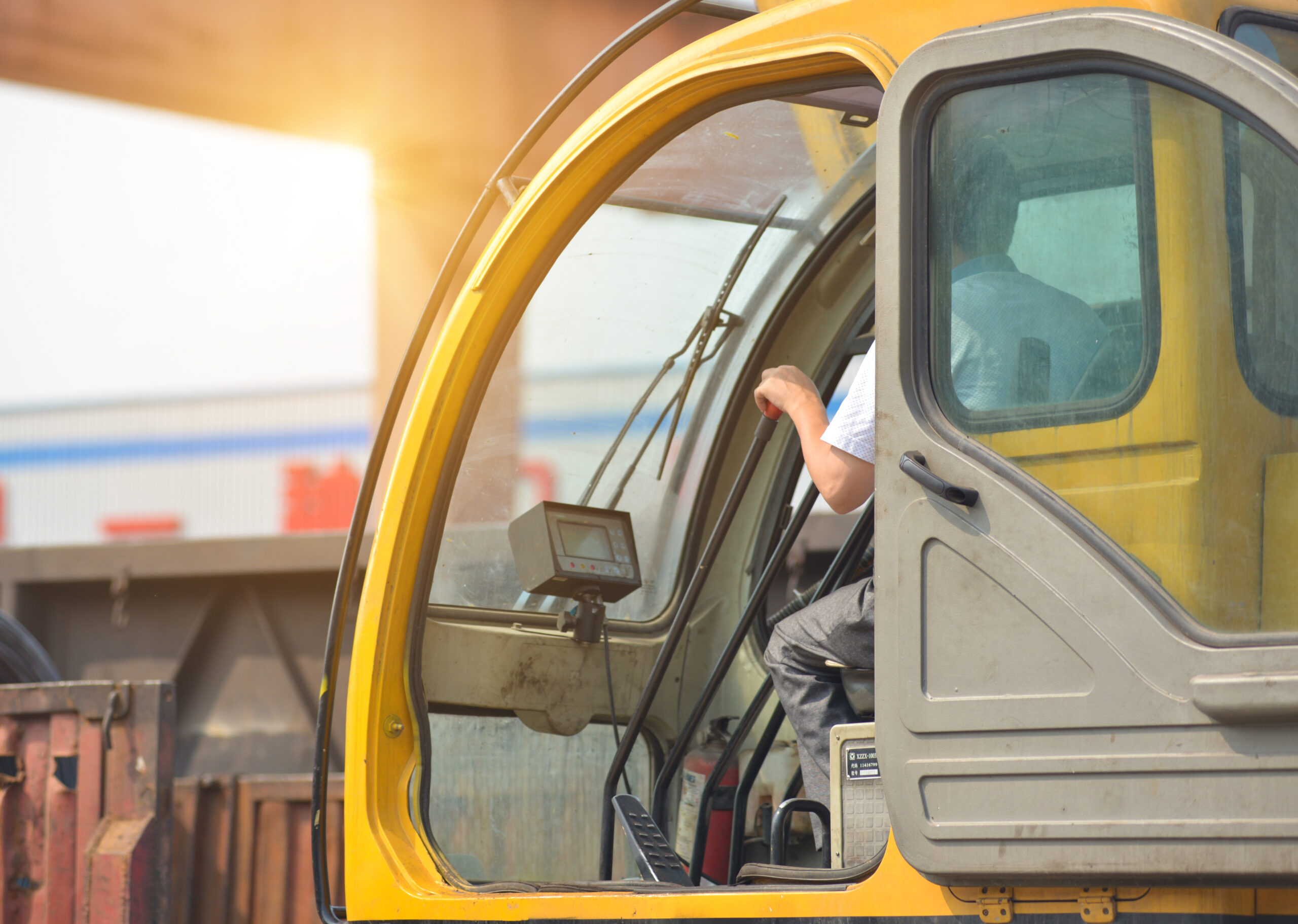
In an era where industry is called upon to become increasingly efficient, digital, and sustainable, a deep understanding of the meaning of retrofit is essential for those aiming to innovate without replacing. Derived from the English terms “retro” (backward) and “fit” (to adapt), retrofit refers to the upgrading or modernization of plants, machinery, or vehicles through the integration of modern technologies capable of enhancing performance, safety, and durability.
In this context, industrial retrofit emerges as a strategic lever for extending the life of existing systems, optimizing production assets, reducing costs and downtime, and ultimately boosting competitiveness in an ever-evolving market.
Industrial Retrofit: Types of Interventions Compared
Retrofit in the industrial sector encompasses various types of interventions, each aimed at renewing specific aspects of a machine or system, depending on operational needs and the level of obsolescence identified.
Technological retrofit involves upgrading control systems, automation platforms, and human-machine interfaces. This type of intervention introduces new functionalities, improves operational accuracy, and aligns machinery with modern industrial standards.
Electrical retrofit focuses on replacing or upgrading outdated electrical components—such as motors, control panels, or inverters—with more efficient and modern solutions. The goal is to optimize energy consumption, support sustainable operations, and enhance the reliability and lifespan of systems.
Mechanical retrofit addresses the structural and mechanical components of machinery, with the aim of improving load capacity, precision, wear resistance, and overall durability.
Software retrofit includes updating or replacing control, monitoring, and management software. This ensures better integration with digital systems, optimized data handling, and more efficient maintenance processes.
These retrofit types are often combined in a single project to enhance performance without the high costs and long timelines associated with replacing entire systems.
Key Sectors and Applications for Retrofit Solutions
Industrial retrofit applies to a wide range of sectors, each with unique demands for efficiency, reliability, and regulatory compliance. It offers tailored solutions to enhance and extend the value of existing systems.
In the metalworking sector, retrofitting CNC machine tools helps modernize lathes, milling machines, and machining centers. By replacing outdated controllers with advanced digital systems, it improves precision, productivity, and flexibility.
In industrial logistics, material handling, and the offshore sector, electrical retrofit for forklifts, cranes, and conveyor systems enhances performance, boosts safety, and reduces energy consumption through the integration of inverters and smart sensors.
As concerns energy and industrial plant sectors, retrofitting industrial machinery and electrical panels improves energy efficiency, operational stability, and compliance with safety regulations—often supported by remote monitoring software and predictive maintenance tools.
In automotive and special vehicles, retrofit upgrades vehicle control and safety systems—such as those in trucks and cranes—extending service life and improving energy performance through electrical and mechatronic modernization.
Retrofit solutions for machine tools are also widely used in the food, chemical, pharmaceutical, paper, and printing industries, where process optimization, automation, and compliance with sector-specific regulations are essential.
What Is the Difference Between Retrofit and Revamping?
Although often used interchangeably, retrofit and revamping follow different logic. Retrofit involves integrating modern technologies into existing systems with the goal of improving performance, safety, and efficiency—often surpassing the original design parameters and incorporating advanced digital systems.
The meaning of revamping, on the other hand, translates into a more conservative approach. Originally used in the railway sector to describe the overhaul of outdated train cars, revamping focuses on restoring machinery and systems to their initial functional condition, without necessarily updating their technological architecture.
In summary, while revamping restores worn or outdated equipment to working order, the original meaning of retrofit lies in transforming existing assets into more advanced systems, ready to meet the challenges of modern industry.
The concrete Benefits and the Meaning of retrofit for Companies
Implementing retrofit solutions for industrial machinery and systems provides companies with numerous strategic advantages that go well beyond routine maintenance, including:
- Cost reduction
. Upgrading existing equipment is significantly more cost-effective than purchasing new systems. Retrofit maximizes initial investments and increases return on capital.
- Improved efficiency. The integration of modern technologies allows for optimized production processes, reduced energy consumption, and substantial long-term savings.
- Enhanced safety. Advanced control systems and monitoring devices increase operator protection and reduce the risk of operational errors or accidents.
- Compliance. The meaning of retrofit lies in ensuring that outdated equipment, when properly upgraded, complies with current safety and performance regulations—thereby avoiding penalties and guaranteeing safe, lawful operations.
- Environmental sustainability. Retrofit enables more efficient resource management, supporting environmental goals and contributing to a more sustainable future.
Ultimately, industrial retrofit not only improves system performance, but also helps companies maintain a competitive edge, aligning operations with global innovation and sustainability demands.
Legislation and Regulations on Industrial Retrofit
Every retrofit intervention is subject to specific regulations to ensure that system upgrades do not compromise safety, reliability, or environmental compliance.
1. Health and Safety Regulations
When applied to cranes and heavy machinery, industrial retrofit must primarily comply with workplace health and safety standards, including:
CE and ISO Standards
European directives and international standards—such as ISO 12100, which governs machinery safety—regulate interventions on existing systems to ensure every modification adheres to defined safety criteria.
Machinery Directive (2006/42/EC)
In the European Union, this directive outlines requirements for the design, construction, and maintenance of machinery. Any technical upgrade, including those related to retrofit, must comply with these provisions to ensure legal conformity.
Anti-tip Safety Standards
Retrofit work involving cranes, lifting equipment, or similar machinery must meet specific anti-tipping requirements, essential to protecting operators during use.
2. Environmental Regulations
Companies must also ensure that retrofit activities do not increase emissions, noise pollution, or other environmental impacts. Retrofit is therefore governed by strict environmental standards, covering: energy efficiency requirements, electronic waste regulations, proper disposal of obsolete components.
For instance, when an industrial plant or piece of machinery is upgraded with energy-efficient technologies, the retrofit must comply with national and international standards on energy efficiency. Moreover, any outdated components replaced during the process must be disposed of according to local regulations for electronic and industrial waste.
3. Authorizations and Certifications
Relevant authorities may mandate specific authorizations or certifications, depending on the type of system or machinery undergoing retrofit.. In some cases, third-party verification by certification bodies is necessary to confirm full regulatory compliance.
4. Legal Responsibility and Corporate Obligations
Companies must be aware of their legal responsibilities in the context of retrofit. If the system does not meet safety standards or if the retrofit is carried out improperly, the company may be held liable for damages or accidents. To avoid this, several key steps are essential:
- Maintain detailed documentation of all updates (e.g., compliance tests, certifications, updated manuals).
- Rely only on qualified professionals who work in accordance with current regulations, ensuring safe and legal upgrades.
- Monitor ongoing maintenance, ensuring that retrofitted systems remain compliant over time.
The Meaning of Retrofit according to 3Bmust: Experience that Renews
With over 15 years of experience, 3Bmust International has become a global reference point in the retrofit sector. Internationally recognized for our expertise in electronic system upgrades and anti-tip safety systems, we deliver cutting-edge solutions that extend the operational life of equipment without the need for replacement.
Our retrofit kits are deployed in highly complex environments—including offshore, port, and construction sectors—demonstrating the reliability and flexibility of a service built on competence, innovation, and maximum safety.
Thanks to a wide range of ready-to-ship retrofit kits, we can ensure fast interventions on equipment with standard configurations. For more complex needs, we develop custom solutions, designing dedicated components and tailored electrical panels.
Choosing 3Bmust means partnering with a reliable, skilled company that can help you preserve and extend the efficiency of your machinery over time.
Explore our retrofit catalogue and contact us for a customized solution!
No comment yet, add your voice below!